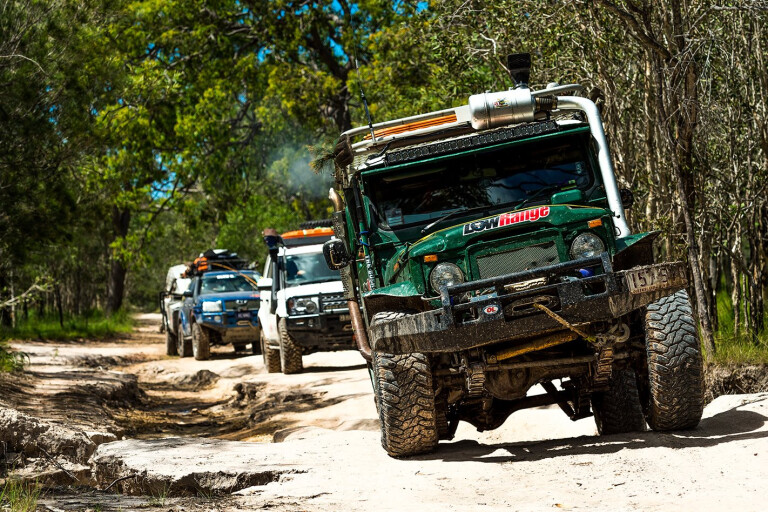
IT’S FUNNY, isn’t it? Last month we had a yarn about metal fatigue, and I showed you some of the damage on Milo’s front panel. But then when I went to make another one, the first thing I had to deal with was another form of fatigue.
No, not the sort that sees the average mudflatter with his head on the bar late at night after a rather long counter lunch. Nope, this time it was rubber fatigue in the MIG welder.
If I sound surprised, it’s because I was. See, I bought that MIG more than 15 years ago after putting in buckets of research to make sure I got the right one. It’s the first MIG I’ve ever owned and will probably outlast me. So I guess this column is a bit of a yarn on what to look for when you’re spending money on tools. And it’s written by someone who’s wasted so much money on tools over the years, he should know.
I started collecting tools as a lad. My 14th birthday present was a set of Sidchrome sockets – Whitworth-sized, because I had an old BSA. I’ve still got them, and still use them. They’re a bit rusty maybe, but good tools can last a lifetime. At 16, with a toolbox full from farm sales and things bought when needed, I made the biggest investment of my life: a stick (or arc) welder, because I wanted to weld some mounts to my FJ to take a red motor.
These days you can buy stick welders anywhere, from Big W to the web, but back then, especially in the country, there wasn’t a lot of range. In fact, in my town I had a choice of two, and one was an industrial model so expensive I could have bought another dozen or so FJs for the same money. That’s not saying much: the average price of an FJ in 1973 was about $50.
This was still slightly more than I earned in a week, and the smaller welder still cost me three weeks’ work. It was a Liquid Arc, made in Australia, and although it looks like total crap, it still works.
I got lucky, because in those days in a small town no business could survive selling stuff that didn’t last. Strangely enough, last time I passed through there, there was a dollar shop selling rubbish where the old hardware store used to be. Times change, eh?
That little Liquid Arc taught me to stick weld, which meant I could always make a buck in the bush; in the ranks of bush mechanics, you’re judged by how good your own welding looks. Starting young is an advantage!
Along the way I learnt gas welding, too, although the gas usually got used more for cutting, brazing and bending. Still, armed with both, I could pretty much do anything. So, even though the world had shifted to MIG welding, I just stuck to the old stick.
Then, faced with a whole stack of panel welding back in the days when I first built Milo, I figured it was time to invest in an MIG and learn how to use one. I looked at various models, asked people who used them daily – like my mate Cooky who builds custom exhausts – and did a bit of homework on the principles behind gas shielding. I wound up yarning with a bloke called Greg from State of the Arc.
Here’s the first trick: If you’re going to make a real investment in tools, go to a specialist (forget about the combination 52-piece toolkit you get for $12 at Aldi). In my case, that meant travelling a couple of suburbs away to Capalaba. Greg was a boilermaker in a past life and exactly the sort of bloke who knew about welding. He recommended buying the largest single-phase MIG in the shop, which was a lovely bright red Lincoln.
I baulked at the price – even if it was only half that of a rusty FJ – but he told me the same factory that made Lincolns under licence here in Australia also made its own brand – much the same thing but at a better price. That brand was Liquid Arc. With happy memories of the back seat of the old FJ, I gladly put in an order.
The ‘new’ MIG worked brilliantly every time I needed it, until I plugged it in to do the job pictured here. Then it spattered and sparked and generally behaved like one of us had lost the plot. It gave plenty of gas, so the wire feed was right, but the test welds looked like bird shit.
So I rang State of the Arc and asked to speak to Greg. I figured after 15 years he’d probably moved on, but he was still there. Good shops are like that. I was only halfway through describing my problem when he said: “How old is it again?” He told me that the rubber gas line was probably past its use-by date, so none of the shielding gas was getting to the handpiece. Then he told me how to fix it.
After a bit of mucking around and sourcing some old fuel line, I was back in business. I was so chuffed I figured I’d drop over to State of the Arc with a slab of XXXX. I would have, too, except the old bike wouldn’t start until I’d swapped out the battery – and the 10mm spanner and Phillips driver from the Aldi toolkit had turned to cheese.
So if you’re planning on mucking around with machines for a lifetime or two, good tools are worth every penny. Next month I’ll tell you how things went with the new front panel!
COMMENTS