Prime Planet Energy And Solutions (PPES) is a battery manufacturing company co-owned by Toyota and Panasonic that marries the electronic brand’s battery know-how with Toyota’s automotive industry nous.
Following a feasibility study in 2017, the joint venture began in 2019 with batteries rolling out in earnest since 2020.
The operation - 51 per cent owned by Toyota - now employs 8400 people in Japan and China.
We’re the first media (outside of Toyota Times) to get a glimpse inside its flagship Himeji production facility in Himeji, almost 600km to the south of Tokyo.
With only one battery-electric vehicle currently in market (and that's not yet in Australia after being pushed back to Feb 2024), the outward image of Toyota is one of a company that’s failed to heed the shift towards BEV that was kick-started by Tesla, with Musk’s company reaping the rewards of being first.
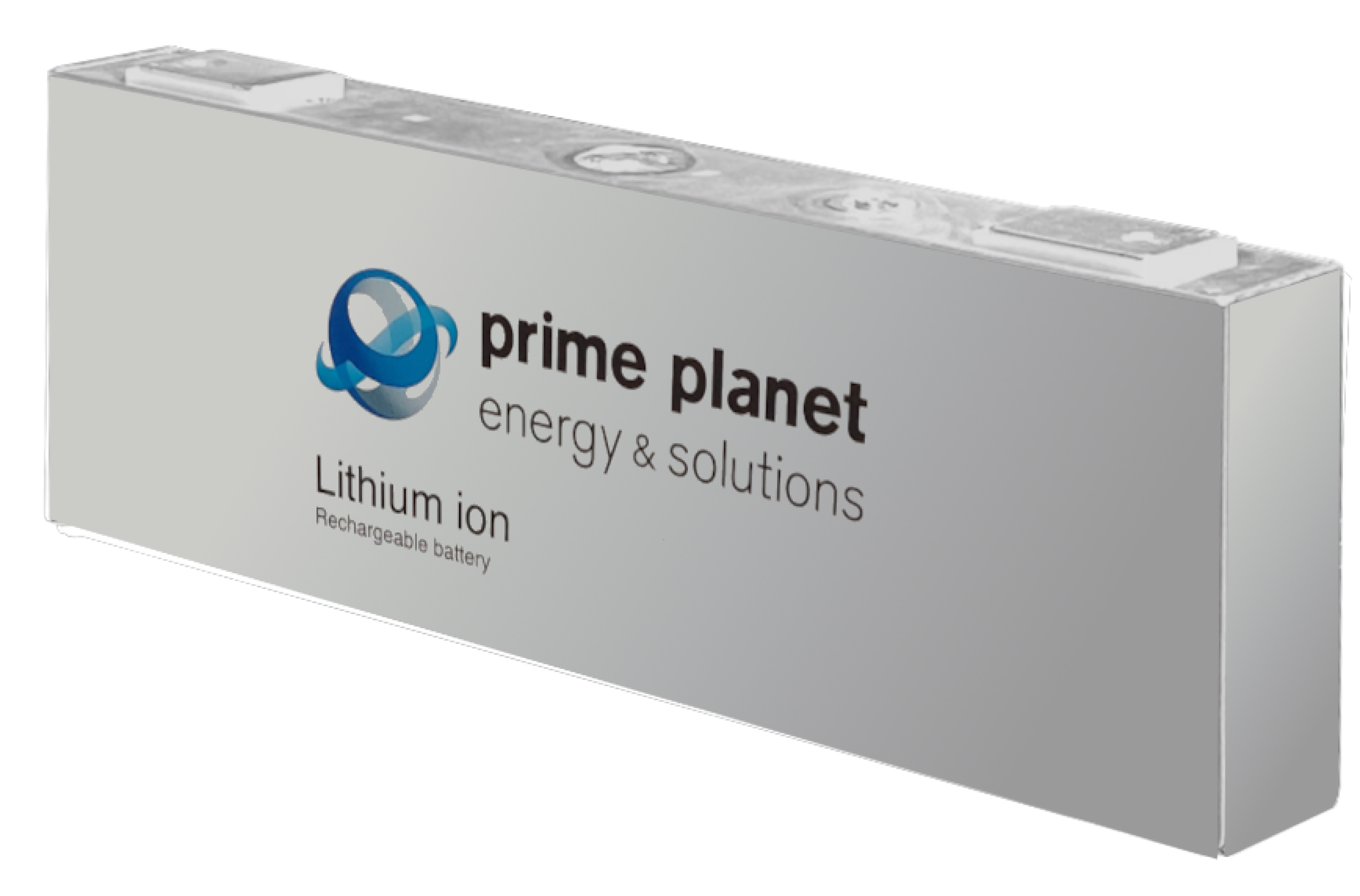
Other early adopters are also kicking goals, with BYD and MG’s BEV sales speaking volumes.
Toyota Australia claims it isn’t interested in being first, though. Its cautious approach comes from wanting to get the recipe right and not damaging the brand’s reputation for reliability in the process.
“Currently, Toyota Motor Corporation’s R&D spending and capital investment is approximately three trillion yen a year, or more than A$31 billion – and growing," Toyota Australia's Vice President of Sales, Marketing and Franchise Operations Sean Hanley tells Wheels.
“On its own, the R&D component is some $13 billion a year. That works out at almost one-and-a-half million dollars [being spent] every hour of every day”, he emphasises.
“But here’s the rub. No matter how much we increase our upfront investments, I have to tell you that not even Toyota can do everything alone. That’s why our partnerships are so important.”
The big difference between PPES’s approach and competitors, says Toyota, is attention to detail.
Before battery packs or stacks are shipped off to customers, the charging, discharging and aging process takes 20 days, compared to the 10 days that other manufacturers allow.
This naturally slows production and adds cost but for a good reason.
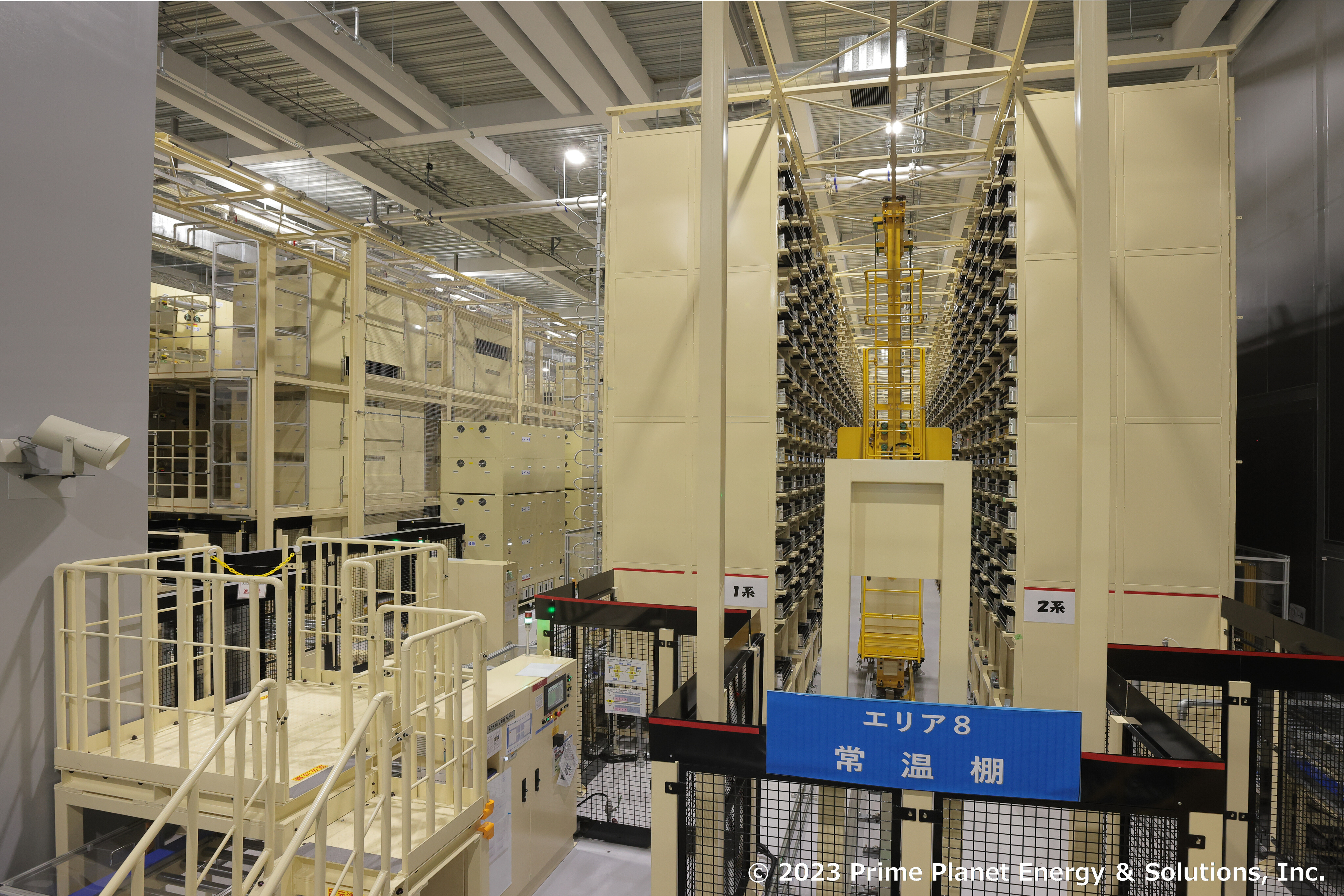
Despite estimates from RedBook showing that a Tesla Model 3 (68-73 per cent) will have higher residual values in three years than a mainstream sedan such as the Toyota Camry (59-60 per cent) or a luxury sedan like the BMW 3 Series (50-53 per cent), Hanley is adamant that Toyota’s greater battery longevity will give the BZ4x – and future models – a leg up when it comes to overall ownership.
What’s the scale of the facility?
The perfectly rectangular - and frankly monolithic - Himeji structure measures 225m wide, 430m long and 56m high, with the capacity to produce 80,000 71.4kWh NCM batteries for the BZ4x annually.
Battery cell production capacity (for Toyota) at Himeji will swell by 7GWh in 2024, claims the company. That’s roughly equivalent to 100,000 current BZ4x packs, or more than double the current production levels.
Packs for the BZ4x are also manufactured at other PPES facilities across Japan.
The facility itself is pristine and largely empty of humans. For the BZ4x batteries, raw materials for the anode and cathode are processed and flattened to as little as 2 micrometres thick, before being wrapped tightly into individual units.
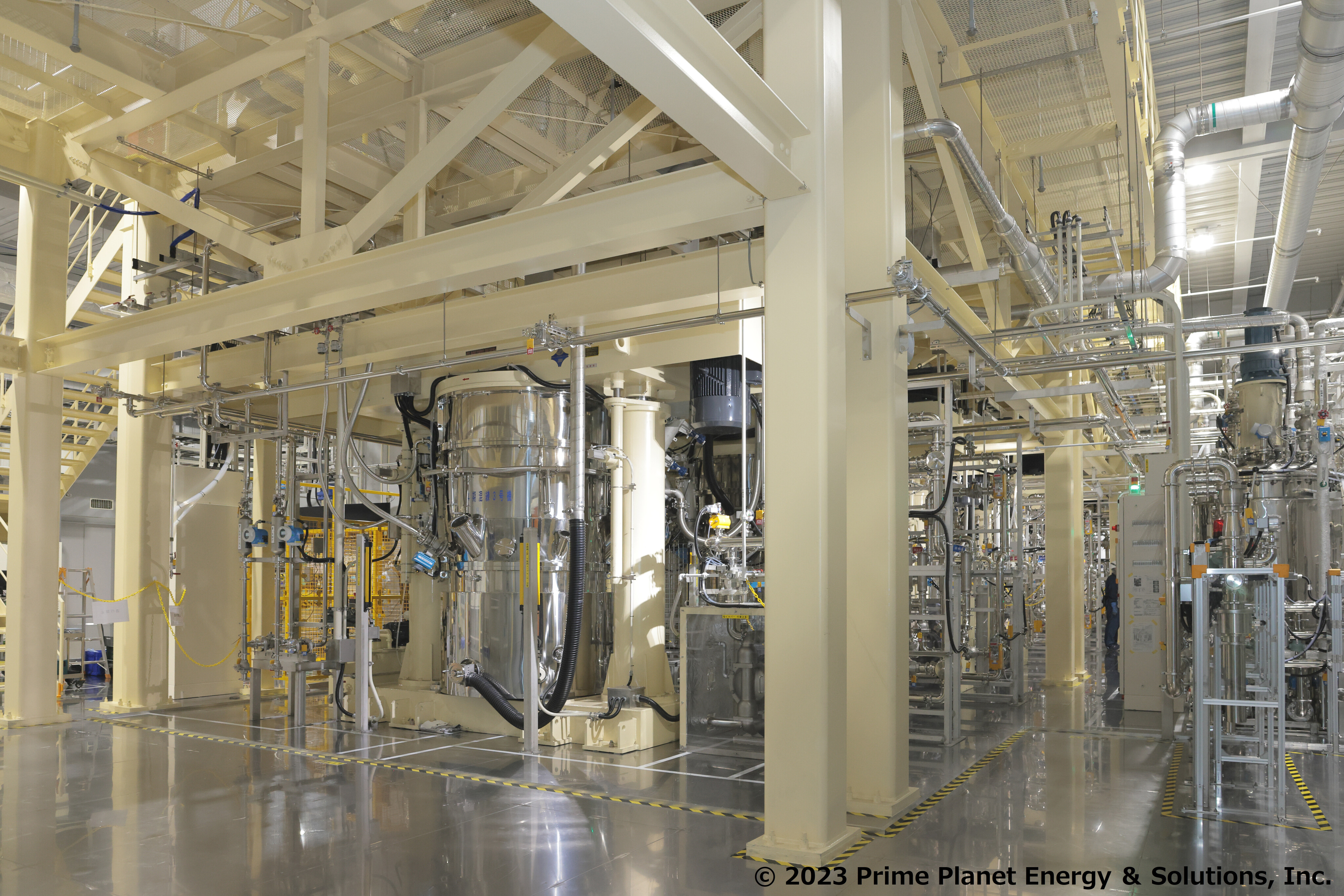
Three of these units are bundled into a casing, multiples of which are formed into a stack after the electrolyte is added.
The raw materials come from a host of places, notably nickel mined by BHP in Western Australia.
PPES currently sources the bulk of its lithium from Argentina and Chile, though as supply chains are revisited Australian-sourced lithium could eventually feature.
Currently, there are limited numbers of recycled materials in the BZ4x’s battery, though the copper foil and connectors are 100% recycled materials, and the anode contains a percentage of recycled materials.
PPES is still locking down recycled material suppliers and is working to increase the percentage of recycled materials it uses in production.
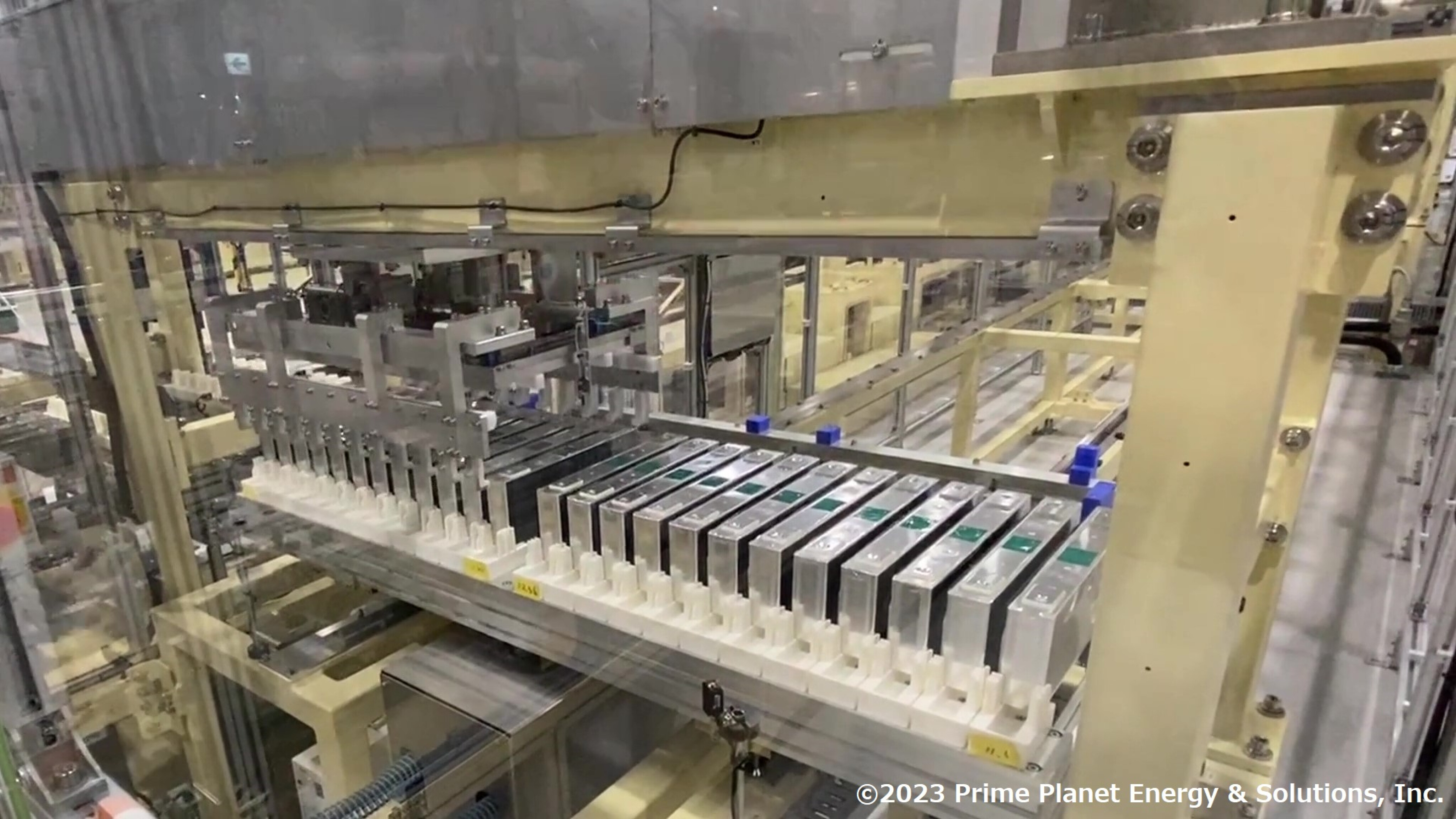
What does the future hold?
There’s plenty of talk that solid-state batteries are the endgame, but we’re not there yet. And in the meantime, there’s plenty of work to do on the current technology.
At one end, Toyota and PPES are both looking to drastically cut emissions created by battery manufacturing.
By 2030, it’s keen to have zero emissions from power production used by the plant – meaning it will be fully powered by renewable energy.
PPES is also aiming to slash supply chain emissions by 80 per cent before 2030.
Technology advancements are also key. With solid-state batteries not expected until 2027 at the earliest, the world needs other options in the meantime.
By 2026, the team wants to have a high-performance ‘monopolar’ battery for flagship products rolled out and in production.
The claim? A 200 per cent jump in range compared to current lithium-ion batteries, along with a 20 per cent cost reduction and a 20-minute charge time.
Next will be a ‘popularisation’ battery; a more affordable lithium-ion phosphate chemistry (currently used by carmakers including Tesla) that offers 20 per cent more driving range than today’s lithium-ion batteries but at 60 per cent of the cost, and with a 30-minute charge time.
Finally, nickel-heavy chemistry will bring further improvement over the 2026 Performance battery, according to the company.
It’s targeting another 10 per cent improvement in range, the same cost drop and a similar ultra-rapid charge time.
Toyota will be detailing technology improvements to its BEVs over the coming week as it gears up to show off a host of concepts at the Japan Mobility Show. Stay tuned for more details on the brand’s increasingly electrified future.
COMMENTS