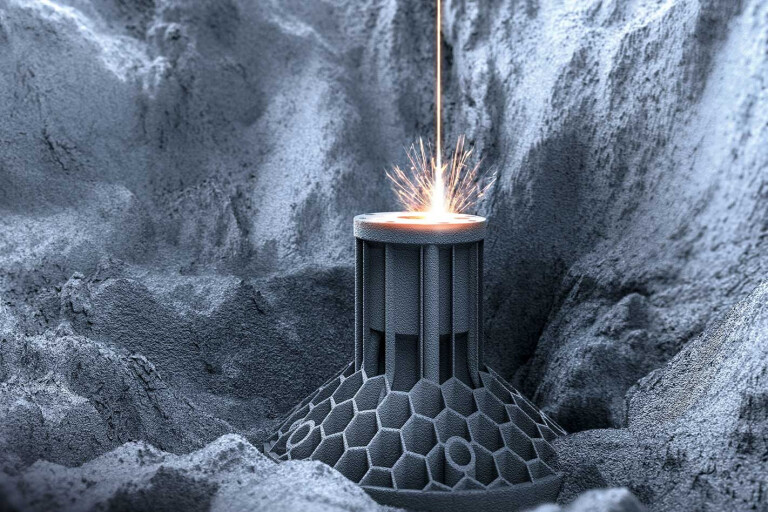
More than one million, that’s how many 3D-printed components BMW has produced in the last 10 years, not that you’d know it. While most people know 3D printing by its common name, BMW, Mercedes, and Porsche refer to it by its technical name, additive manufacturing.
It's a rapidly growing area of automotive manufacturing but companies have been taking the technology seriously longer than most realise. In fact, BMW estimates that last year its output of additive-manufactured parts, around 200,000, was 42 per cent more than in 2017. 3D printing isn’t just for building model figurines anymore.
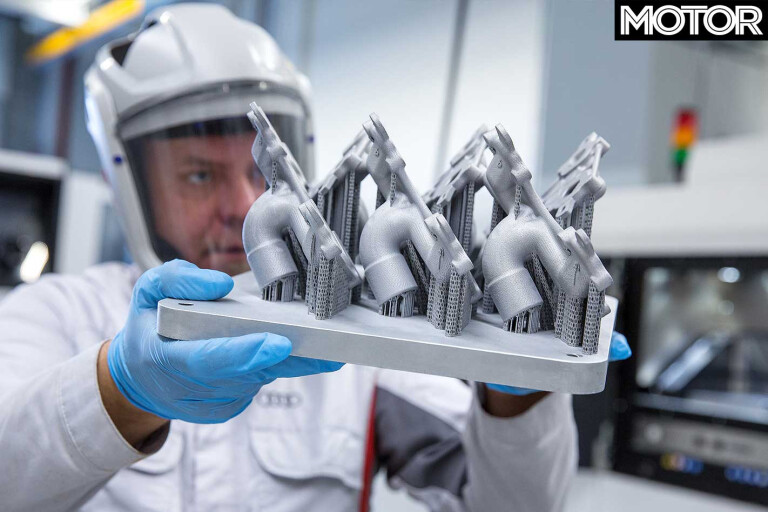
There are several different additive manufacturing processes but the two most commonly used in the automotive world involve a powdered version of the intended material, usually a metal alloy, and a laser to fuse it into form. Porsche describes one such process as ‘the powder and nozzle procedure’.
In this method, powdered metal is directed through a nozzle (like water from a hose) to a point where it meets a laser beam and there it is fused as the nozzle and laser move to create the part.
The second, and apparently more manageable of the two, is the powder bed system. In this process layer by layer of powdered material is laid across an existing bed of the same material, while a laser above fuses the sections it needs from each layer to continue the shape underneath.
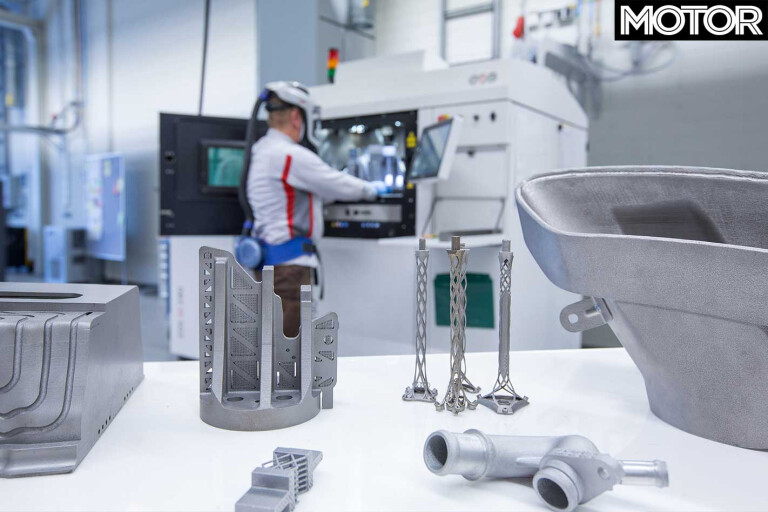
This leaves plenty of excess powder surrounding the final product but allows almost any design or shape to be constructed. Explained another way, if a cylinder were to be created using this method, the laser would only need to fuse a circle in each new layer of powder, on top of the existing fused metal. The un-fused powder would remain around this circle, on each layer, to support the next layer.
Put simply, in the words of Dr Masahiko Mori, chairman of machining and tooling company DMG MORI, “additive manufacturing materialises engineers’ ideas, and makes it possible to produce well-thought-through designs from the digital world in the real one.”
Where traditional manufacturing is limited by the tools and raw materials used, the possibilities for additive manufacturing are essentially limitless. For example, constructing a chain without needing to weld the links closed is practically impossible using traditional manufacturing, but it’s far easier when using powder and lasers.
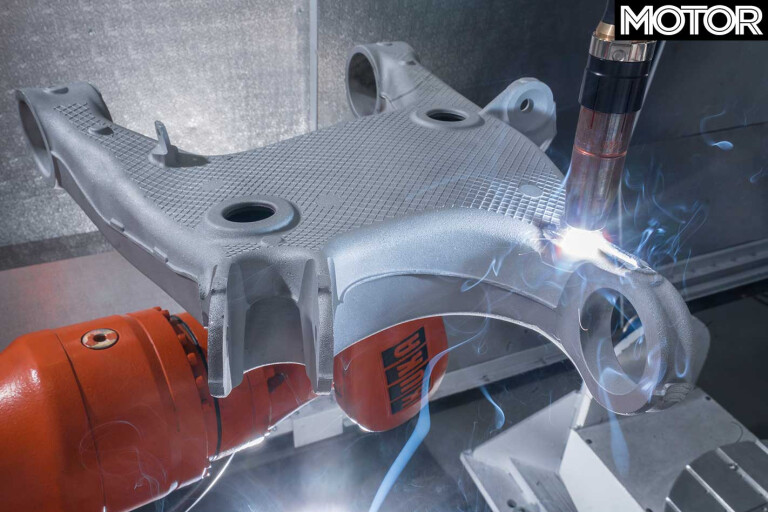
But why do manufacturers want to put precious resources into something that’s still being refined? It comes down to the advantages which brings us back to BMW’s millionth part. That component was a guide rail for an i8 Roadster window, the second aspect of the car that is now ‘3D-printed’.
The first was the roof fixture. BMW says these aluminium alloy parts are both lighter and stronger than an injection-moulded plastic part. The Bavarian brand goes as far as saying additive manufacturing is to become a “key part” in its car-making process. Rolls-Royce even has a total of 10 parts it manufactures using this process.
Of course, in the world of technology, there are those who wish to take a new concept as far as it can be stretched. In 2014, US-based Local Motors took its ‘Strati’ car for a test drive, claiming it was the first entirely 3D-printed car, mechanicals aside. Though Local Motors has yet to release it as a tangible commercial product, Porsche is looking to get bolder with its own use of additive manufacturing.
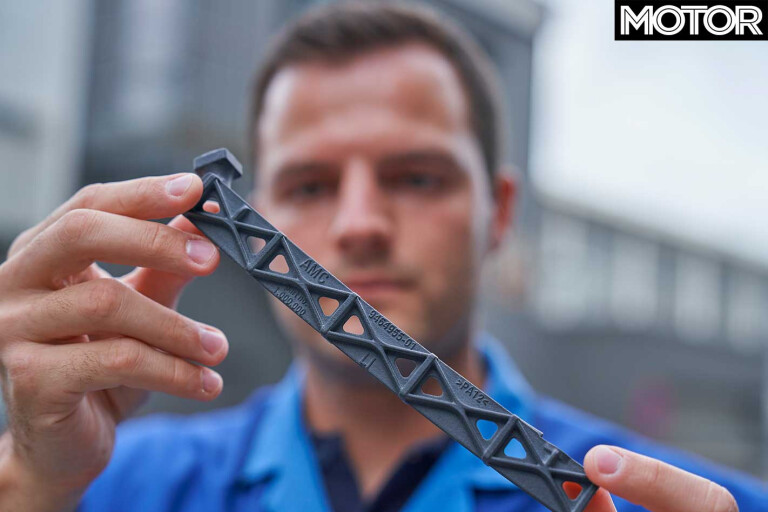
The Porsche powertrain department has tested a rotor shaft for an electric motor, printed over thirteen hours to a quality it says wouldn’t be able to be replicated on a lathe, due to a complex strengthening structure inside the shaft.
Porsche says it has no plans to completely 3D print a car, even in the distant future, but says additive manufacturing is a big step forward in saving resources, creating stronger parts, and allowing more design freedom. The important part? That all adds up to better sports cars in the future.
Real World 3d Printing examples
High-end stoppers
Even Bugatti is no stranger to the world of additive manufacturing, last year creating a titanium brake caliper. At the time Bugatti claimed it was the largest functional 3D-printed component ever created from titanium.
Intricate rims
US wheel company HRE has begun using a process it calls Electron Beam Melting to create incredibly complicated wheel designs that could not have been achieved using traditional methods.
Plant growth
Porsche says it’s experimenting with using plant-based materials in its additive-manufactured parts, and has already built door panels made from plant fibres. It says the result isn’t quite right just yet, but stay tuned.
COMMENTS